デジタル印刷機が市場に導入されて久しいです。印刷機をメインにした展示会などでは、その多くがデジタル印刷機になっており、すでにさまざまなものが発表され、導入された印刷会社もかなり多くなっています。
当社ではIndigo 6000シリーズを2台保有しており、導入当初からシールやシュリンクを含むラベル関係、および軟包材において多数の実績を得ています。導入当初はキャンペーン品やパーソナライズ製品が多かったのですが、次第にデジタル印刷機の特徴を活かした多品種中小ロットの仕事が増え、最近では環境への関心の高まりを背景に更に注目度が増してきています。そこで環境配慮への観点から、当社が保有するデジタル印刷機を見ていきます。
社会環境の変化
環境面において、レジ袋の有料化が2020年7月に義務づけられるなど、海洋プラスチック対策への関心は益々高まっており、すでに成果も見え始めています。図1は産業廃棄物の過去数年における排出量とその処理状況である。排出量は減少傾向にあるものの、ほぼ横ばいとなっています。
また、図2はその内訳ですが、この中で廃プラスチックは平成28年度実績でいえば、387百万t中の1.8%となるおよそ7百万tです。
一方、一般廃棄物の過去数年の排出状況(図3)は、平成29年度では4,289万tとなっていて、ピークとなる平成12年度と比較するとおよそ2割減少しており、排出されたゴミの約11.7%はプラスチックとなっています(図4)。
これは消費者の意識の向上と共に、薄肉化などさまざまな企業努力によりその成果が見え始めているものと思われます。ただし、一般廃棄物の処理の約80%は焼却されており(図5)、今後気候変動への対策とも相まって、ゴミの削減はますます企業側の大きな責任になることが予測されています。印刷を行う原反の多くにプラスチックを使用し、同じものを大量に作ることが命題であった我々印刷業も同様です。
その対応の一つとして、当社が保有するデジタル印刷のメリットについて以下に記します。
デジタル印刷機Indigo 6000シリーズ
図6はデジタル印刷機Indigoの構造図です。左の中央にあるのが、主な操作を行うタッチパネルで、この位置が丁度オペレーターの胸の高さあたりなるため、印刷機本体の規模感は想像していただけるかと思います。
本機で全色の印刷を行え、かなりコンパクトな印刷機です。紙巾は狭く印刷速度も遅いため、大ロットには不向きですが、多品種小ロットには小回りが利いて、その威力を発揮します。
ー関連資料を無料でダウンロードする
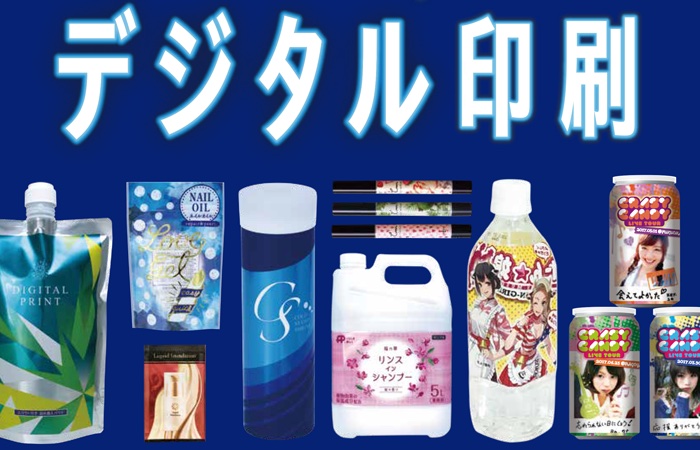
環境問題と包材ロスデジタル
環境問題の対策として、3Rへの取組みがある。Reduce(リデュース)、Reuse(リユース)、Recycle(リサイクル)の3つのRの総称ですが(最近ではこれにRenewableを加えて4Rが一般化している)、その最初に挙げているReduce(リデュース)とは、製品をつくる時に使う資源の量を少なくすることや廃棄物の発生を少なくすることです。
ところが従来のアナログの印刷機は同じものを大量に作ることを一つの命題としており、これまでは印刷速度や色数の多さを競い合うような場面もしばしば見られました。また軟包装材を例に取ると日本では今もグラビア印刷が主流で、機械も大型のものが多く紙巾も多岐にわたるため、原反を他の製品と共有することは難しいのです。
原反の最低購入量は原反毎にほぼ決まっており、例えば3,000m必要でも4,000mの購入が必要で、不必要な1000mは最終的には廃棄されるのが一般的でした。
プラスチック循環利用協会の資料によると平成29年の廃プラは前年比4万t増の903万tで、うち57万tは加工ロスとされている1)。この全てが包材要因ではありませんが、相当量のロスが生じていることは容易に想像できるでしょう。
これはもはやフードロスならぬ包材ロスといっても過言ではありません。
デジタル印刷は必要な時に必要な量だけの生産が可能で、またスタートロスもほとんど発生しないため、この加工ロスを最小限に抑えることが可能となります。これはReduce(リデュース)への一つの回答となり、同時に在庫問題も発生しません。
仕様の統一
軟包材を製造するコンバーターにとって、これまで仕様の統一は大きな課題でした。同じような中身と寸法であるにも関わらず、過去の包材の立上げ時の経緯などから、その構成は多岐に渡ります。
当然、包材とその納入先の充填機との相性の問題もあって、そのような結果になったものと思われますが、立上げから何年か経つと、顧客側もコンバーター側もその経緯が不明確になってしまい、その後充填ラインが改良されても構成は従来通りで、絵柄のみを変更して新製品として販売されるケースは、今なお多いのではないでしょうか。
デジタル印刷の仕事は小ロットのものが多く、グラビアで多岐に渡っている構成をそのまま転用すると、様々な種類の原反を用意しておかねばならず、効率が悪くコストも高くなってしまいます。
そのため個別に構成を決定する場合には従来の構成を参考にはするものの、改めてゼロベースで顧客の要望を聞き、中身に応じた構成案を提示します。そうすると、例えば「アルミ箔を使っていれば構成は作りやすいもので一任します」という回答を実際に多く得られることがあり、驚かされます。もちろん小ロットの仕事で、かつそのために製袋納入が多いことが最大の要因ではあるのですが、自然と仕様は統一されロスの削減にも有効なのです。
特色レスについて
仕様の統一と同じようなことが刷色についてもいえます。グラビアであれば明らかに特色で再現するような絵柄でも、デジタルではCMYKと白が基本となります。これまで印刷立ち会いなどでかなりの時間を費やしていた顧客でも事前にグラビアとデジタルの特徴についての説明、校正などを提示し了承を得ていれば、問題になるようなことはありません。アナログ印刷において特色は、インキの在庫や残肉管理を含め、頭を痛める問題でした。デジタル印刷の浸透を契機に市場が特色レスに理解を示せれば、大きな環境対応の方策になることでしょう。
下記は、グラビア印刷とデジタル印刷それぞれの主な長所・短所を簡単に示しています(表1)。
まとめ
デジタル印刷を用いた環境への取組みの一端について述べさせていただきました。デジタル印刷の利点はまだまだ多くあります。例えばインキはVOCを含まず、版を使わないため切り替えロスもほとんど発生せず、刷版の廃液処理もありません。昨今小ロット多品種化は急速に進み、今後デジタル印刷は形を変え、用途も広がってくるでしょう。当社としては包材ロス削減を積極的に推進し、デジタル印刷技術を武器に環境を意識しつつ、一歩先の包材のあり方を考えて行きたいと思います。
Pro-perでは、小ロットからオリジナルのパッケージ作成や、環境に配慮したパッケージ作成など、お客様のニーズに合わせてデザイン、印刷、加工まで専門スタッフが丁寧に対応いたします。
パッケージに関するご質問やご相談がございましたら、お気軽にPro-perまでお問い合わせください。
参考
・1)プラスチック循環利用協会 (参照2020-1-15
・2)日本HP (参照2020-1-15)
関連商品
記事を作成・監修したマイスター
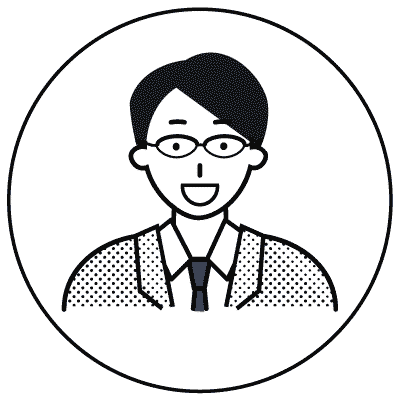
吉田 潤一
福島印刷工業株式会社
マーケティング部 開発室長
資格:包装専士
1986年よりパッケージ印刷業界に従事しております。長年培ってきたパッケージ印刷に関する知識を活かし、当社の加工技術や製品情報をご紹介します。
趣味 は フォークソング、オヤジバンドでライブ活動をすること。